Impact!
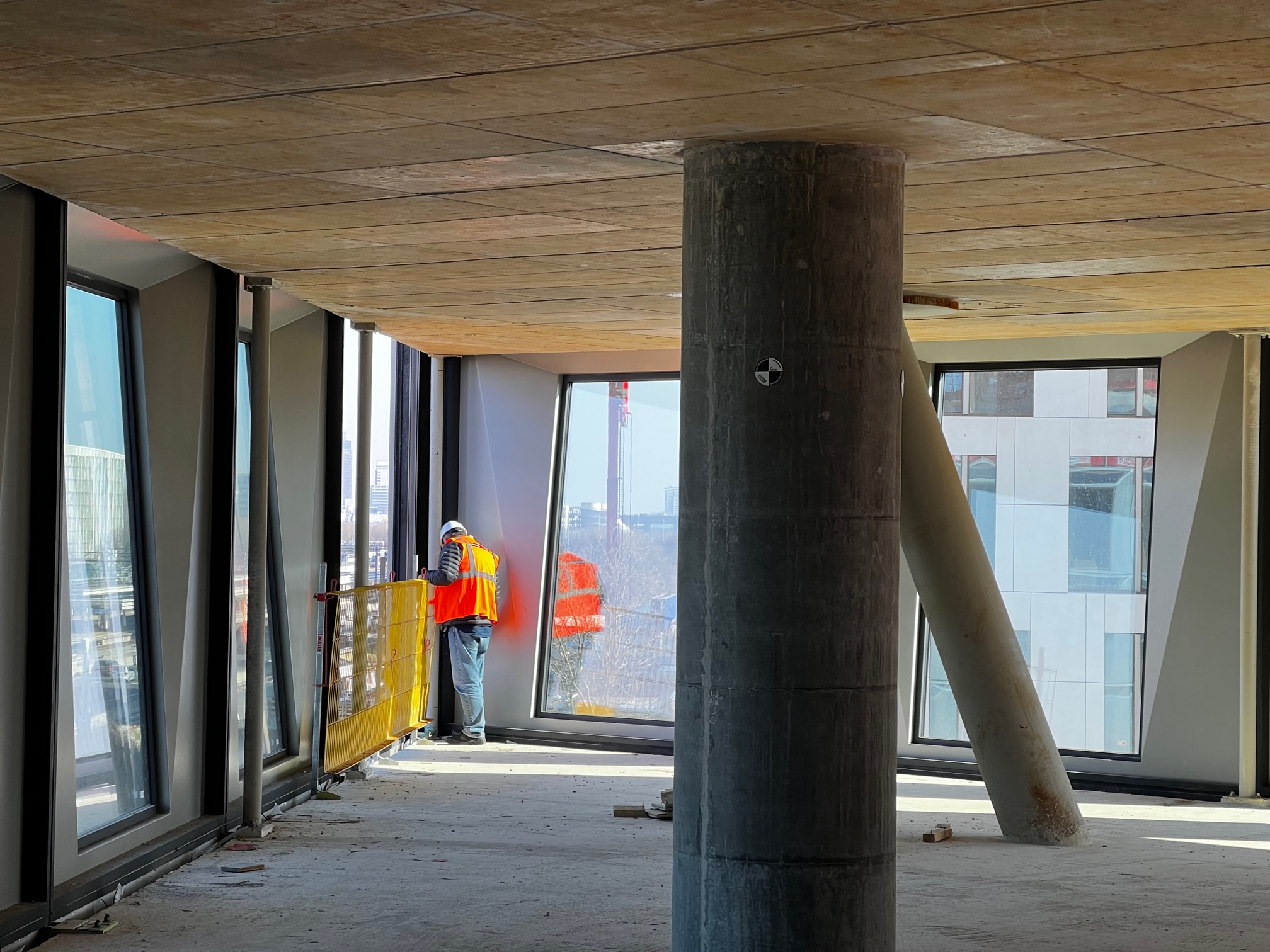
Dromen van een wereld vol herbruikbare en biobased materialen
Sven Erik Janssen ziet zijn toekomst in biobased bouwen
Een gesprek met:
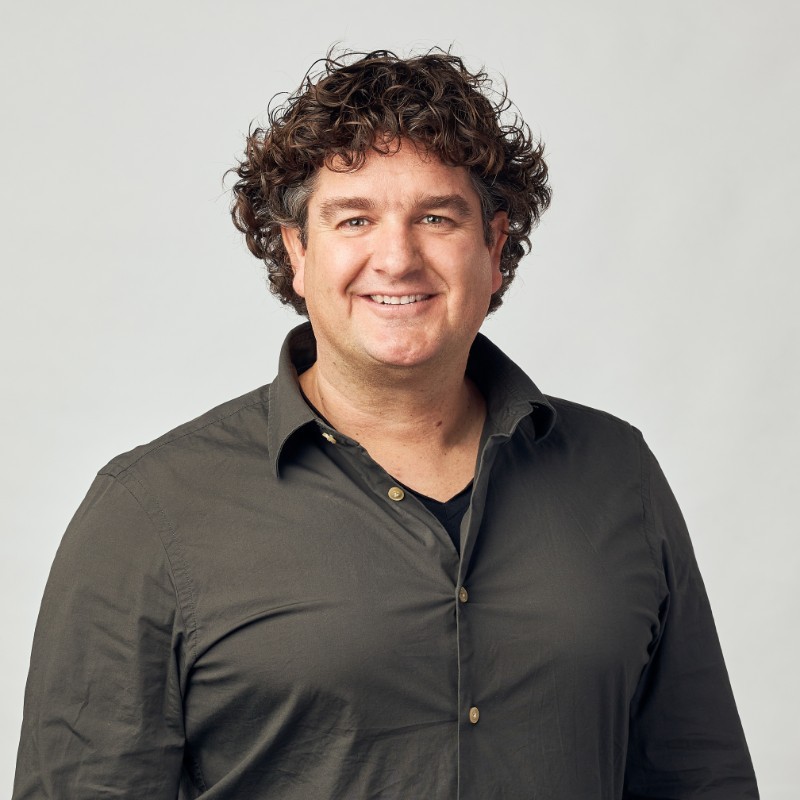
Sven Erik Janssen
Sven Erik Janssen, één van de eigenaren van Holland Composites heeft een helder toekomstbeeld voor ogen. “De ideale wereld is een wereld die volledig gebruik maakt van herbruikbare en biobased materialen.” Met het materiaal Duplicor, een bio based composiet, zet Holland composites de eerste stappen op weg naar zo’n wereld.
De oorsprong van Holland Composites ligt in de jachtbouw. Echter, sinds enkele jaren richt Holland Composites zich in toenemende mate op de bouwsector. “Denk aan het toepassen van lichtgewicht composietmaterialen in de bouw”, vertelt Janssen. Inmiddels heeft het bedrijf al flink wat spraakmakende projecten van hun producten voorzien. Voorbeelden daarvan zijn de gevels van het Stedelijk Museum in Amsterdam en de opvallende composiet gevel van Tivoli Vredenburg in Utrecht.
Biobased
Alle kennis en ervaring die Holland Composites in de afgelopen jaren heeft opgebouwd is nu vertaald in een nieuw biobased composietmateriaal dat ze onder de naam Duplicor op de markt brengen. “Ons materiaal”, legt Janssen uit, “vindt zijn oorsprong in plantafval. Denk aan steeltjes van suikerriet en maïsresten. Die persen we tot een zeer hoog thermische en zuurbestendige biohars. Vervolgens voegen we dat samen met een glasvezellaminaat in buiten toepassingen als gevels en daken. Voor binnenwanden kan Duplicor ook natuurvezels bevatten. Als isolatie kern in een sandwich element, gebruiken we gerecyclede petfoam. Dat is geen bio product, maar we zijn wel bewust afgestapt van het gebruik van PUR, PIR, EPS foams en toxische kunstharsen in onze composietproducten. We gebruiken feitelijk de plastic soep in de vorm van PETfoam als thermisch isolerende laag in onze gevel en dak constructies van Duplicor.”
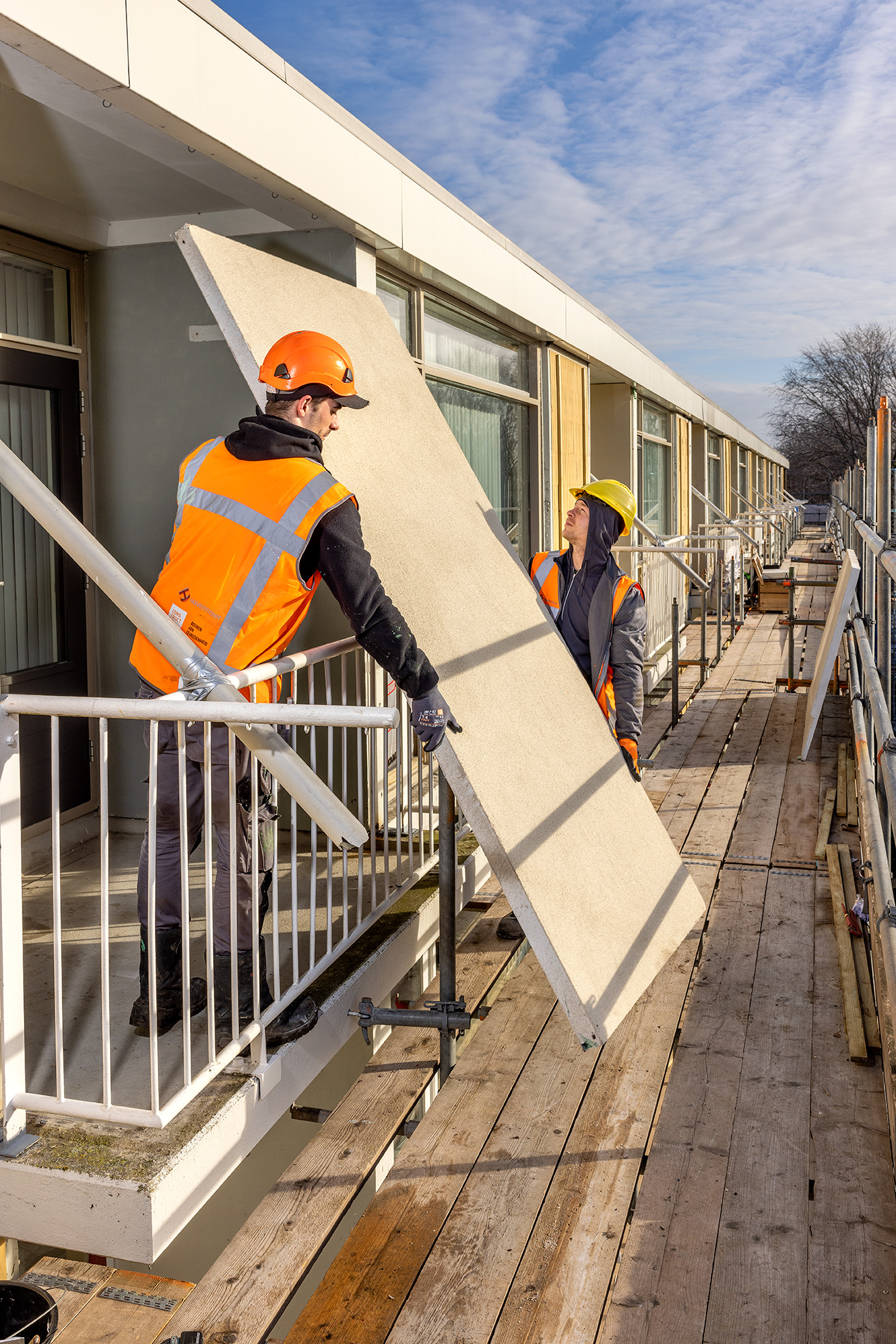
Lichter
Wat het product vooral bijzonder maakt, is dat het een stuk lichter is dan reguliere bouwmaterialen. Janssen wijst erop dat een vliegtuig omgerekend uit 350 kilo high performance materialen per persoon bestaat. “En dan vliegt het ook nog eens zo’n 1000 kilometer per uur. Een gebouw waar we in wonen en werken bestaat al gauw uit 55.000 kilo per persoon aan beton, staal en allerhande andere conventionele bouwmaterialen.” Daarmee vergeleken springt Duplicor als bouwmateriaal er dan ook positief uit. “CE Delft heeft een LCA-studie heeft gemaakt. Ze hebben daarbij vooral gekeken naar de CO2 equivalent per kilogram aan product. Daarvoor analyseerde ze een typische gevel met een isolatiewaarde van 5,8. Daarvoor hebben wij een paneel van 172 millimeter dikte nodig met een totaalgewicht van 24 kilo per vierkante meter. Om eenzelfde prestatie met bijvoorbeeld een betonnen gevel te kunnen leveren heb je een dikte van 400 millimeter nodig en dat komt neer op een gewicht van 450 kilo per vierkante meter.” Tel uit je winst in bruikbaar vloeroppervlak per gebouw laag en minder gebruik van materialen.
Minder materiaal
Hij wil er maar mee zeggen, dat er voor het bouwen met zijn product flink wat minder materiaal nodig is. “Sterker, zo’n ranke gevel scheelt pakweg vijftien tot twintig centimeter vloeroppervlak per verdieping. Geloof mij, met dit soort getallen zit elke ontwikkelaar op het puntje van zijn stoel. Zeker omdat we ook nog eens voldoen aan de hoogste brandnormeringen.”
The Pulse of Amsterdam, een combinatie van wonen, werken en culturele voorzieningen wordt thans met een constructieve gevel van Duplicor opgetrokken. “De gevelelementen van circa vier bij vier meter maken wij in onze fabriek. Het gaat zowel om de isolerende schil compleet met zonnepanelen tot de binnenafwerking waar mensen tegenaan kijken als ze in het gebouw wonen of werken.”
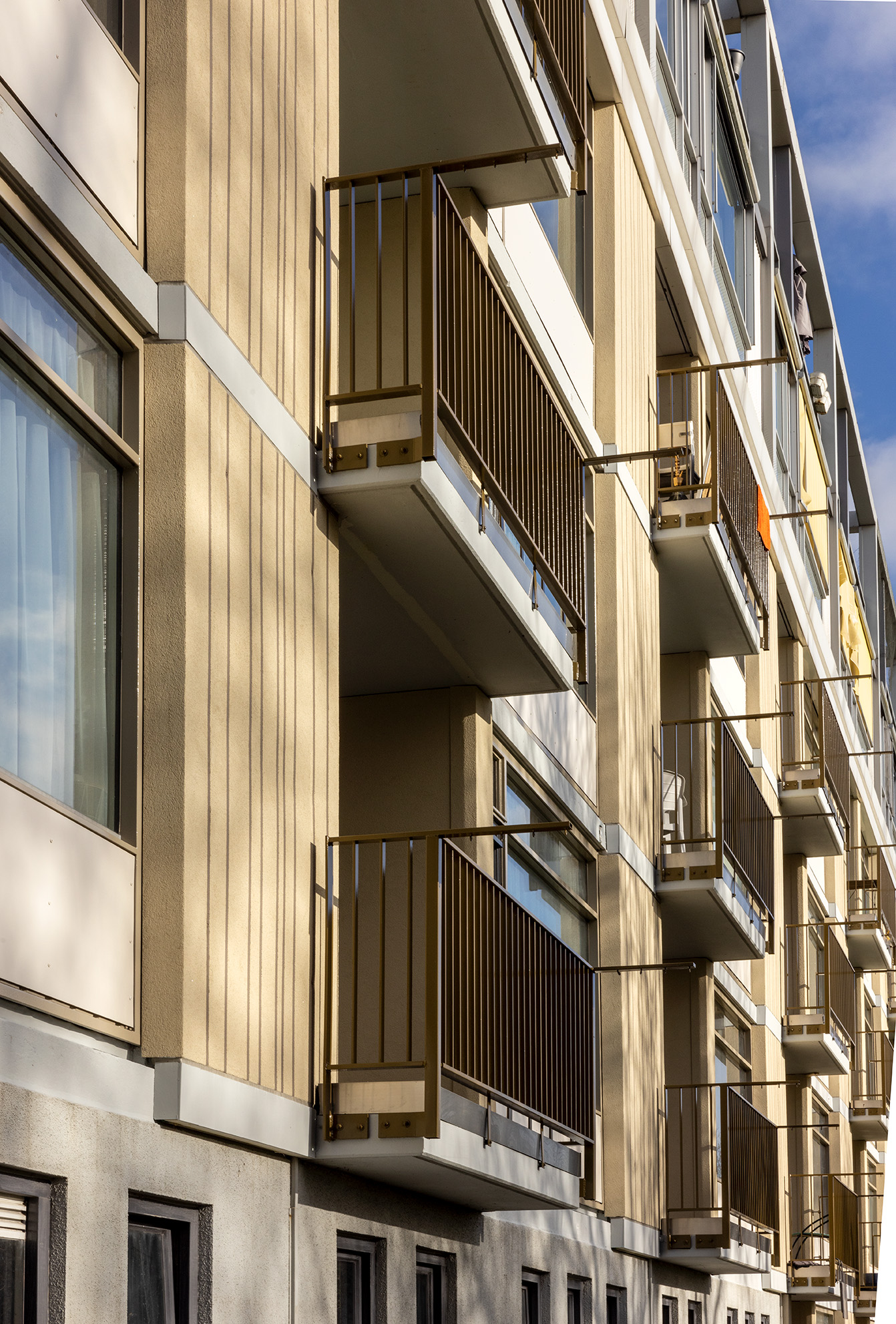
Kortom, het materiaal vindt inmiddels zijn weg naar diverse projecten. Het gaat Janssen echter nog niet snel genoeg. Dat heeft enerzijds te maken met wet- en regelgeving. En anderzijds met de kostprijs. Als het gaat om veiligheid kan de wet- en regelgeving wat hem betreft niet streng genoeg zijn. Het materiaal voldoet volgens hem vooral door die strenge wet- en regelgeving aan alle brandveiligheidseisen. “Maar diezelfde wet- en regelgeving staat nog wel toe dat er materialen worden toegepast die niet goed voor het milieu zijn of zelfs haaks staan op de duurzaamheidseisen. Doe daar iets aan. Schrijf voor dat zoveel procent van de nieuwbouwgevels een bepaalde prestatie heeft. Dan vallen er al een hoop materialen af en het dwingt de architect en de opdrachtgever om aan die eisen te voldoen. Want laten we eerlijk zijn, als we het aan de ontwikkelaar of de eindopdrachtgever laten afhangen dan duurt de transitie naar een CO2 neutrale en circulaire wereld nog wel even.”
Kostprijs
Het gebruik van biobased materialen zou volgens hem ook helpen in het naar beneden brengen van de kostprijs van zijn producten. “Wij innoveren bij de gratie van de orders die we hebben. Zie het als een vliegwiel. Wij werken heel hard vanuit onze fabriek, maar je moet nu met dit materiaal echt naar automotiv achtige bouwprocessen. Om die materiaalprijs, die nu nog hoger is, naar beneden te brengen werken we aan een knetterefficiënt productieproces. Tegelijkertijd”, voegt hij er in één adem aan toe, “vind ik dat opdrachtgevers die hun nek uitsteken ook wel wat geholpen kunnen worden.”
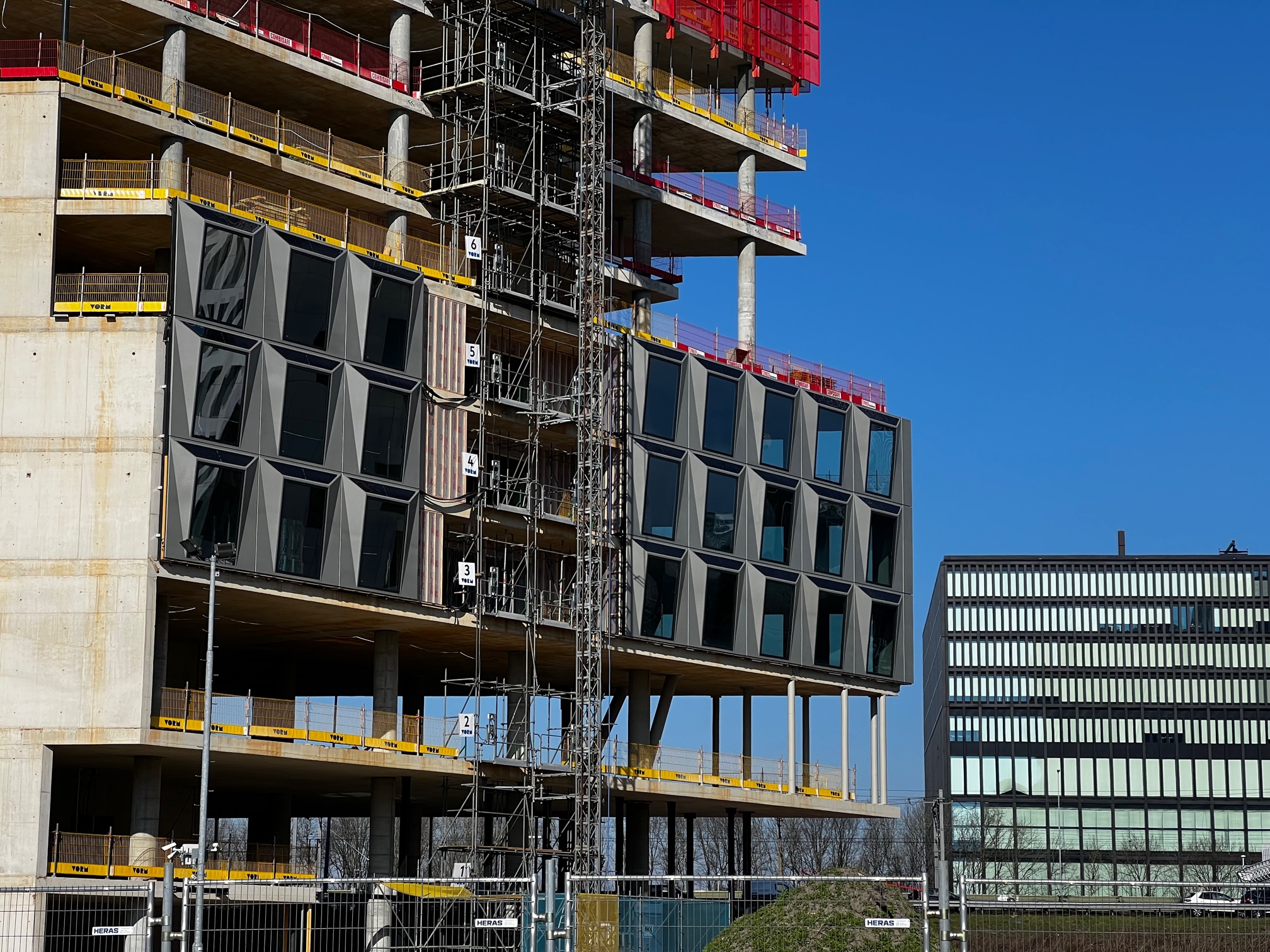
Naast nieuwbouw richt Duplicor zich ook op renovatie. “Daarbij gaat het om het vervangen van daken en gevels. “De gevels voorzien we van de brandwerende en isolerende panelen. Mocht het gebouw aan het einde van zijn gebruikscyclus komen dan kunnen we de elementen hergebruiken of recyclen.”
Modulair bouwsysteem
En tenslotte is er nog het flexibele en modulaire bouwsysteem waar Janssen een groeiende markt in ziet. “We maken geen volledige units in de fabriek maar allemaal verschillende producten als gevel- en dakelementen. Zie het als de Ikeakast die je zelf kunt samenstellen en uitbreiden. Dus een element met een raam, element met een deur enzovoort. Die mix van elementen vormen uiteindelijk samen een woning. Zo gaan we op deze wijze voor een opdrachtgever 99 zorgwoningen van veertig vierkante meter bouwen. In één dag zetten we het hele casco neer.”
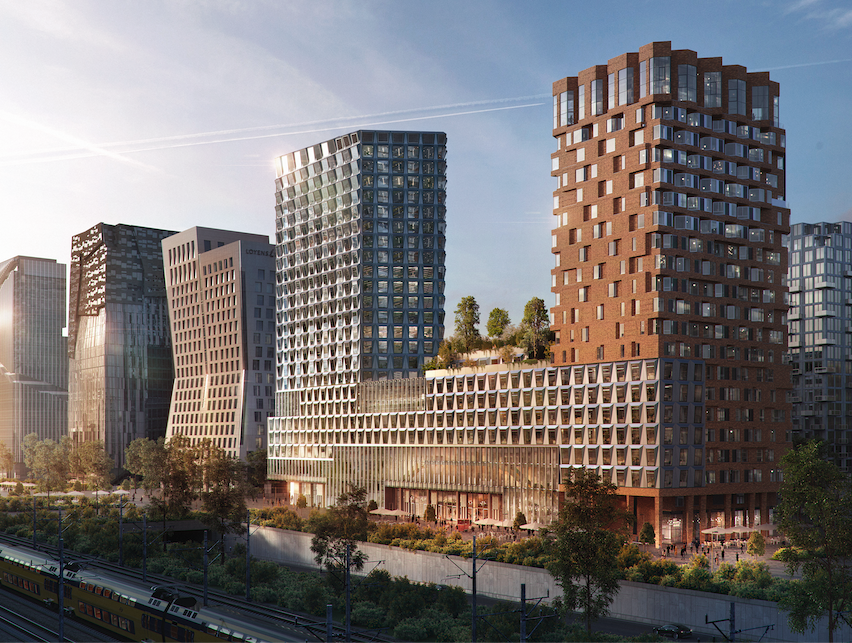
Groot voordeel van deze aanpak is dat het complex ook zo weer uit elkaar kan worden gehaald om elders weer neer te zetten. “We kunnen met dit systeem oneindig flexibel modulair bouwen. En we hebben het ontworpen voor hergebruik. Want”, benadrukt Janssen, “de ideale wereld is een wereld die straks volledig gebruik maakt van herbruikbare en biobased materialen. Daar zijn we het met elkaar toch wel over eens.”
Lees meer artikelen:
Vorig artikel
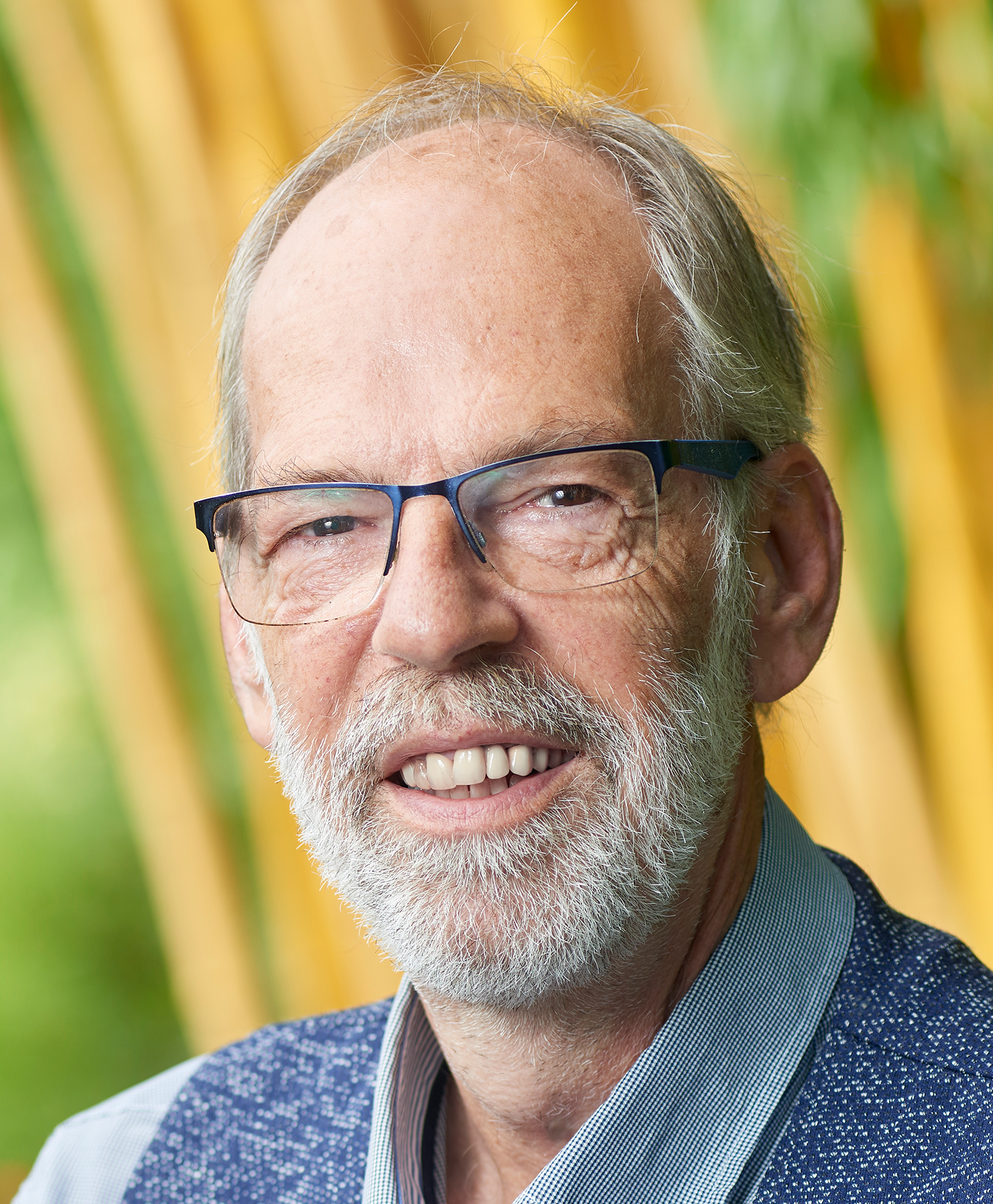
Helft van wereldbevolking woont materiaal-neutraal
Volgend artikel
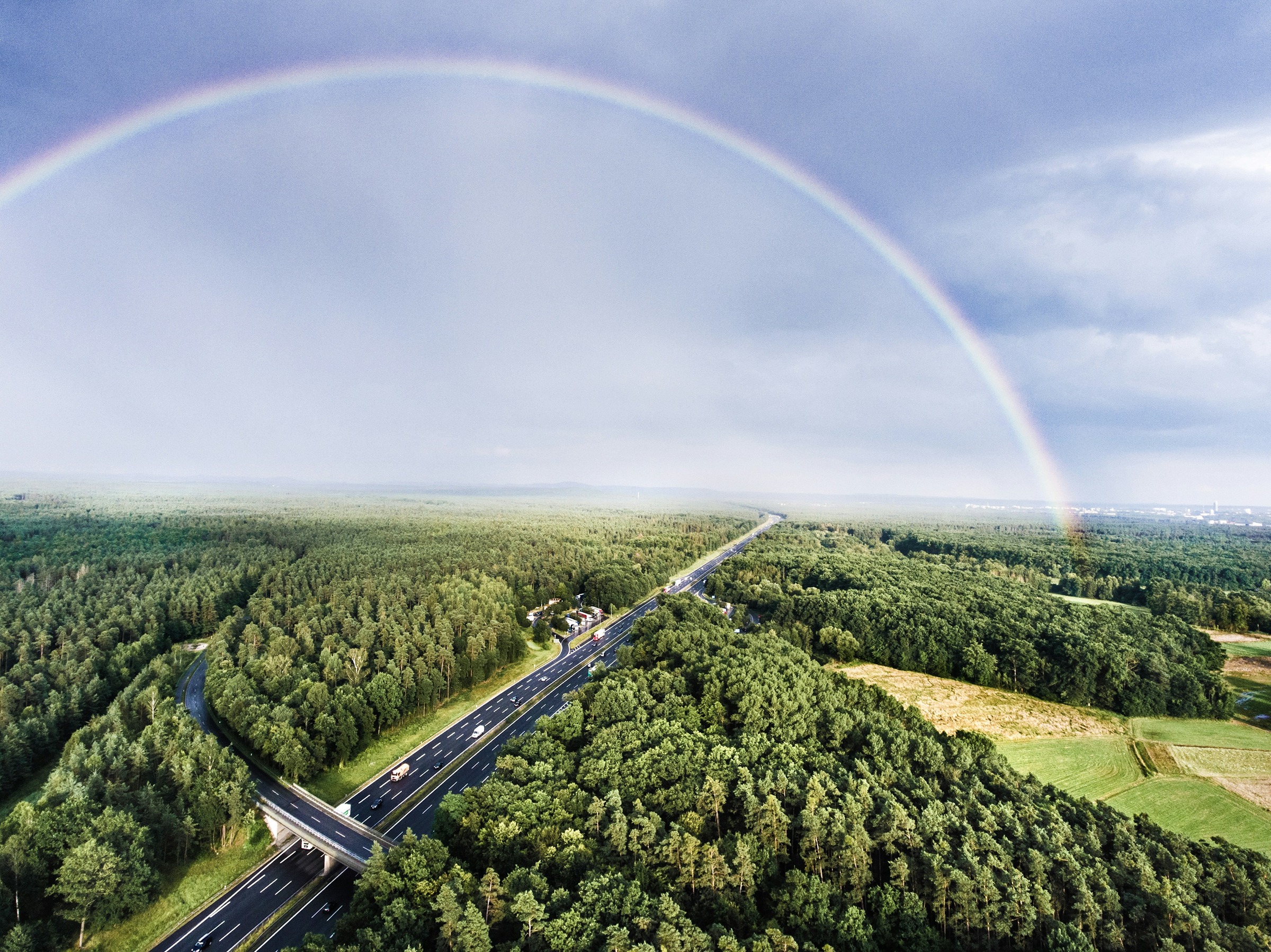